Recognizing Porosity in Welding: Discovering Reasons, Results, and Avoidance Strategies
Porosity in welding is a consistent difficulty that can considerably influence the high quality and stability of welds. As professionals in the welding industry are well mindful, understanding the reasons, results, and prevention strategies associated with porosity is essential for achieving durable and reliable welds. By diving right into the origin of porosity, examining its harmful impacts on weld high quality, and checking out reliable avoidance methods, welders can enhance their understanding and skills to produce high-grade welds constantly. The intricate interplay of aspects adding to porosity calls for a detailed understanding and a proactive method to make sure successful welding results.
Typical Root Causes Of Porosity
Porosity in welding is primarily triggered by a mix of factors such as contamination, incorrect shielding, and insufficient gas insurance coverage during the welding process. Contamination, in the form of dust, oil, or rust on the welding surface, creates gas pockets when heated, causing porosity in the weld. Inappropriate shielding occurs when the shielding gas, commonly made use of in processes like MIG and TIG welding, is unable to totally protect the liquified weld swimming pool from reacting with the bordering air, leading to gas entrapment and subsequent porosity. Furthermore, inadequate gas coverage, commonly due to wrong flow prices or nozzle positioning, can leave parts of the weld unguarded, enabling porosity to develop. These factors collectively add to the development of voids within the weld, deteriorating its stability and potentially creating architectural problems. Understanding and resolving these usual reasons are essential action in protecting against porosity and ensuring the quality and strength of bonded joints.
Results on Weld Top Quality
The visibility of porosity in a weld can dramatically endanger the total high quality and integrity of the welded joint. Porosity within a weld creates gaps or dental caries that damage the framework, making it a lot more vulnerable to splitting, corrosion, and mechanical failure.
Additionally, porosity can hinder the performance of non-destructive screening (NDT) techniques, making it testing to spot other defects or suspensions within the weld. This can cause considerable security problems, especially in critical applications where the structural stability of the welded parts is paramount.

Avoidance Techniques Summary
Given the destructive effect of porosity on weld quality, reliable prevention methods are important to preserving the architectural stability of bonded joints. Among the main avoidance strategies is detailed cleansing of the base materials before welding. Impurities such as oil, grease, corrosion, and wetness can contribute to porosity, so making certain a tidy job surface is crucial. Appropriate storage of welding consumables in dry conditions is also vital to avoid moisture absorption, which can cause gas entrapment throughout welding. In addition, choosing the appropriate welding specifications, such as voltage, existing, and travel rate, can assist reduce the threat of porosity formation. Making sure ample protecting gas circulation and protection is an additional crucial avoidance strategy, as insufficient gas protection can cause atmospheric contamination and porosity. Proper welder training and accreditation are necessary for carrying out preventative actions successfully and constantly. By incorporating these prevention methods right into welding techniques, the event of porosity can be substantially lowered, bring about stronger and more trustworthy welded joints.
Importance of Proper Shielding
Proper shielding in welding plays an important function in stopping climatic contamination and making sure the stability of bonded joints. Protecting gases, such as argon, helium, or a combination of both, are generally used to secure the weld pool from responding with elements in the air like oxygen and nitrogen. When these responsive aspects come into call with the warm weld pool, they can create porosity, bring about weak welds with decreased mechanical buildings.
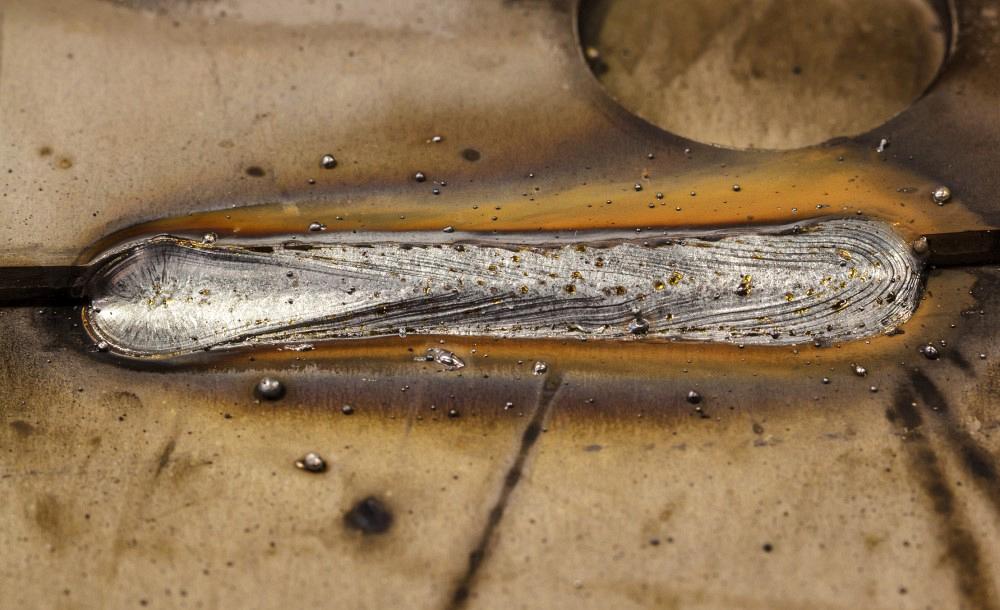
Poor shielding can cause numerous defects like porosity, spatter, and oxidation, compromising the architectural honesty of the bonded joint. Sticking to correct securing techniques is official source vital to create high-quality welds with very little flaws and make certain the durability and integrity of the welded elements.
Monitoring and Control Methods
How can welders successfully keep an eye on and regulate the welding procedure to guarantee optimum outcomes and protect against defects like porosity? By continually checking these variables, welders can recognize variances from the ideal conditions and make instant changes to stop porosity development.

Additionally, carrying out proper training programs for welders is necessary for monitoring and regulating the welding procedure successfully. What is Porosity. Informing welders on the importance of preserving consistent criteria, such as proper gas protecting and travel rate, can assist prevent porosity problems. Routine assessments and qualifications can also make sure that welders excel in monitoring and regulating welding procedures
Furthermore, making use of automated welding next systems can improve surveillance and control capacities. These systems can specifically manage welding criteria, reducing the likelihood of human mistake and guaranteeing constant weld quality. By integrating innovative tracking modern technologies, training programs, and automated systems, welders can properly monitor and manage the welding process to reduce porosity flaws and attain high-quality welds.
Verdict
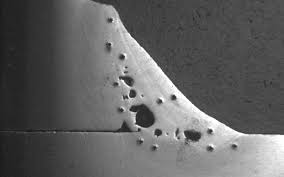